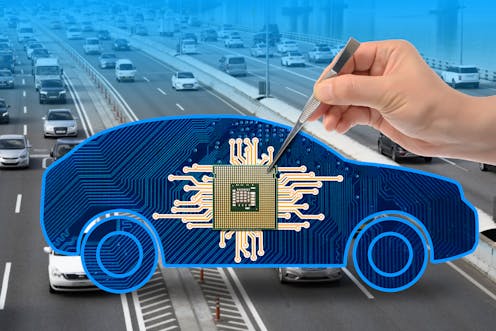
Finally, carmakers got a break. Those in the UK boosted their output by over 13% in February as supply-chain pressures subsided, especially the persistent global shortage in microchips, also known as semiconductors. This “signals an industry on the road to recovery”, declared UK motoring trade association the SMMT. Well, up to a point.
Early in the pandemic, carmakers slashed sales forecasts as demand for cars evaporated, falling 47% in US and 80% in Europe in the first couple of months of lockdowns. Carmakers couldn’t see how sales could rebound quickly, which was a reasonable assumption at the time. In an industry where everyone has their own version of lean or just-in-time manufacturing, where unsold inventories are seen as tantamount to incompetence, they quickly scaled back orders from their supply chain.
Car parts suppliers such as Bosch and Continental reacted by scaling back their production – and naturally, their own suppliers, such as NXP and Infineon, also reduced their forecasts. These second-order effects went deep into the supply chain, eventually converging on the great and mighty semiconductor manufacturer in Taiwan, TSMC (Taiwan Semiconductor Manufacturing Company).
A modern car can easily contain more than 3,000 microchips. These control brakes, doors, airbags and windscreen wipers; they even support advanced functions like driver assistance and navigation control. Chipsets are like golden screws.
Yet obviously, many other industries depend on chips too. At the same time as carmakers were reducing their orders, manufacturers of gadgets such as games consoles, TVs and home appliances were seeing orders surging as consumers were forced to stay at home. They increased their chip requirements, and TSMC was more than happy to oblige.
It then became apparent to carmakers later in 2020 that they had overreacted. But by the time they woke up to this and ramped up orders, it was too late. TSMC was running all of its factories at maximum capacity to meet the surge in gadget demand, and there were no more chips available for carmakers.
As a result of this global semiconductor scarcity, worldwide vehicle production was approximately 11 million units, or about 12%, lower in 2021 than it would otherwise have been.
What carmakers got wrong
No one could have predicted the outbreak of COVID. Nor could anyone have foreseen the ramifications on the supply chain as the virus receded. Still, every executive in the car industry knows the importance of computing power in a modern car. A car is a supercomputer on wheels, they’ll say. And yet they didn’t treat chipsets as a critical area. In other words, they were happy to let their suppliers worry about chip requirements and not have any direct involvement with chipmakers.
Why? Because chips don’t involve mechanical engineering. From the boardroom to the shop floor, carmakers generally focus on final assembly. Chipset design and fabrication is one of many things that gets outsourced.
So during the pandemic, most carmakers had little choice but to perfect the art of triaging their chips: for example, General Motors hoarded them for expensive models, temporarily shutting down factories that produce lower-priced sedans.
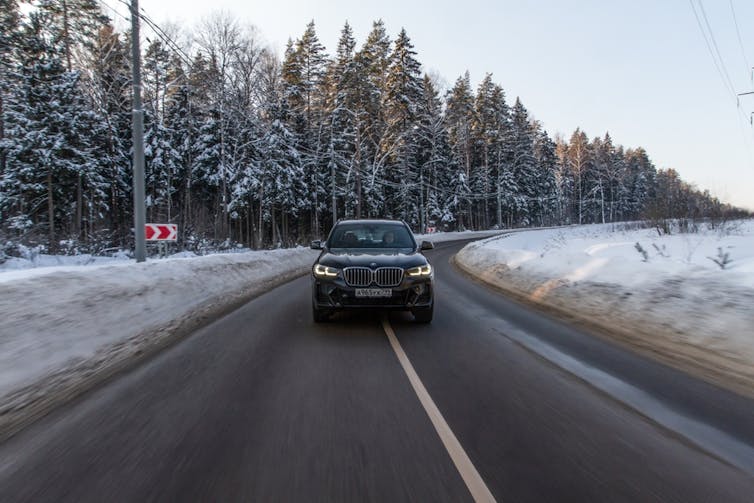
Others instead removed features from vehicles that rely on microprocessors. BMW did away with parking assistance and even touchscreen capabilities in various models. It also withdrew semi-autonomous driving functionality from the X3, its top-selling model. Mercedes-Benz eliminated features such as high-end audio and wireless phone-charging from a number of vehicles.
The future threat
Car production is now increasing as the high pandemic demand for chips for household gadgets has fallen away. Still, it would be unwise to conclude that things are back to normal. Demand for chips is likely to look so different in future as we see the rollout of technologies like AI, the internet of things, and 5G/6G.
Major chipmakers are boosting capacity to meet this extra demand, with big new US facilities in the offing, for example. Yet it will take time for this to come on stream, and it’s still difficult to predict whether it will meet demand.
New product categories can appear unexpectedly, in a similar way to how bitcoin mining suddenly led to unforeseen chip demand. As Professor Rakesh Kumar in the Electrical and Computer Engineering department at the University of Illinois observes: “The exact nature, speed and magnitude of the increase in demand is still unknown.”
As we saw during the pandemic, chip factories also typically run close to maximum capacity, leaving production extremely susceptible to disruptions. Natural disasters like earthquakes and floods can cause problems, as can accidents such as fires and power outages. In March 2021, for instance, a fire at a Renesas Electronics chip factory in Japan caused a significant disruption to supplies over and above the pandemic-related problems. Geopolitical or military tensions, including those between the US and China, could also affect production in future.
The implication is clear: carmakers must cultivate in-house expertise in this area. Rather than relying on suppliers or their sub-suppliers for semiconductors, they need to directly engage with chipmakers and do the relevant designs in-house. For example, Ford announced a collaboration with US chipmaker GlobalFoundries in 2021 to create chips for its vehicles while exploring the prospect of expanding domestic chip production.
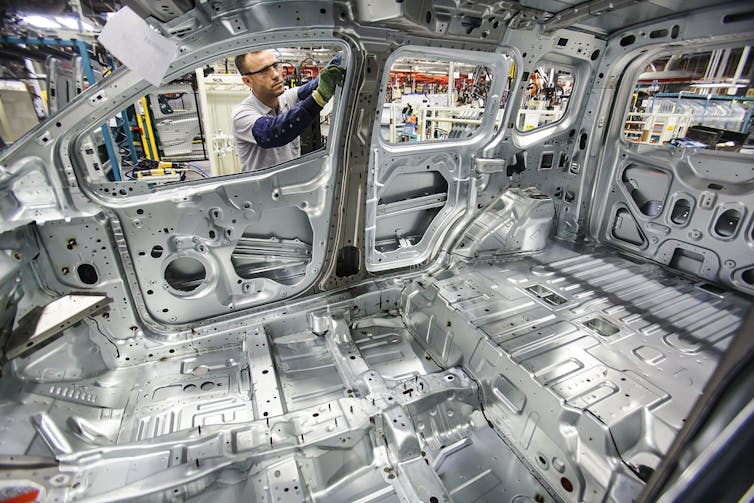
This approach is already common practice among newer, more self-sufficient carmakers such as Tesla and China’s BYD and NIO, who all have extensive operations dedicated to designing or even producing their own chipsets.
These changes will not be easy. Yet the cost of clinging to the status quo will far outweigh the difficulties in the transition. For any company dependent on semiconductors, their resilience and future success hinge on getting this right. The correct response to the end of the pandemic is not to say “back to normal” but “never again”.
Howard Yu does not work for, consult, own shares in or receive funding from any company or organization that would benefit from this article, and has disclosed no relevant affiliations beyond their academic appointment.