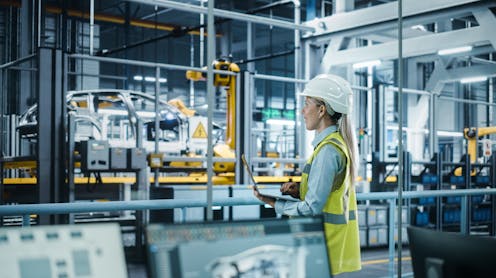
The UK may have lost Eurovision this year, but it recently beat European rivals for an arguably more valuable prize. Jaguar Land Rover (JLR) is expected to build a multi-billion-pound electric vehicle (EV) battery plant in the UK rather than Spain – welcome news for British car makers. After decades of decline, this could help turn Britain into a base for battery production, saving its ailing auto sector.
The news about JLR expected investment brings relief after recent comments from manufacturers including Stellantis (owner of Vauxhall, Citroën and Peugeot), about the future of the UK car sector. These companies are largely concerned about producing EVs under stricter “rules of origin” post-Brexit.
This dictates the duty levied on a product based on where it was made, which could add tariffs on UK cars with Asia-made batteries. According to the rule of origin requirements, a percentage of a “made in Britain” product must be sourced from the UK to be sold without a tariff in the EU.
It’s unlikely that one new battery plant alone will save the UK auto industry, but it’s certainly a step in the right direction. To understand why, it’s important to explain how the UK became an attractive place to make vehicles in the past, when that changed, and why the industry has struggled to reach past highs in recent decades.
The UK automotive industry has travelled a bumpy road during its 130-year history – especially when it comes to production numbers. In the 1950s, the UK was the second largest producer of cars in the world, reaching peak production of nearly 2 million cars a year by the 1970s.
Throughout the 1980s, Japanese car manufacturers built factories in the UK because it helped them to gain a foothold in the lucrative European market. Rules set in 1975 aimed to limit Japanese imports to around 11% of the total UK car sales. Getting around this meant designing cars in Japan and then producing them (which often had English names like Triumph) in the UK to ensure they were exempt from these production caps. Honda started this strategy, but it was so successful that Nissan and Toyota were soon doing the same. In fact, the UK has been home to many major Japanese companies over the years as a result, not just automakers.
Alongside the Japanese-owned car factories, by the turn of the century, Britain’s output was also being bolstered by homegrown brands like Rover and Jaguar – producers of iconic vehicles such as the Land Rover and the Mini. UK production of 1.7 million cars in 2016 doesn’t really come close to the 5 million vehicles produced per year by Germany at this time, but it’s respectable for a nation that was thought to be losing its manufacturing prowess in the 1970s to foreign competition.
Since Brexit, UK car production has been dropping every year, however, reaching a low of 775,000 in 2022. Even before the EU Referendum, manufacturers warned that uncertainty around the future of trade may jeopardise UK factories.
After the UK voted to leave the EU, the government stepped in with investment pledges. But it’s become harder to make the business case for UK auto manufacturing as the realities of Brexit have set in.
British-made batteries
The shift from petrol and diesel engines to batteries is possibly one of the biggest opportunities for the UK to protect what’s left of its auto industry. This is why the JLR battery plant deal is so important. The batteries used to power EVs are large, expensive and difficult to transport because regulators often class them as hazardous materials making transportation subject to strict regulations.
Read more: Electric vehicles: if the UK is serious about being a major player, here’s what needs to happen
The answer to these regulations and the rules of origin requirements is to build battery factories in the UK. Otherwise, the UK simply can’t make anything like the volume of cars it once did. It currently only has the capacity to make enough batteries for 40,000 cars a year.
But EV battery factories are serious undertakings to build and run. Tesla’s “gigafactories” are some of the largest buildings in the world. And after the collapse of the planned British Volt Gigafactory in Blyth in Northumberland, investors are understandably nervous about making such a plan work in the UK.
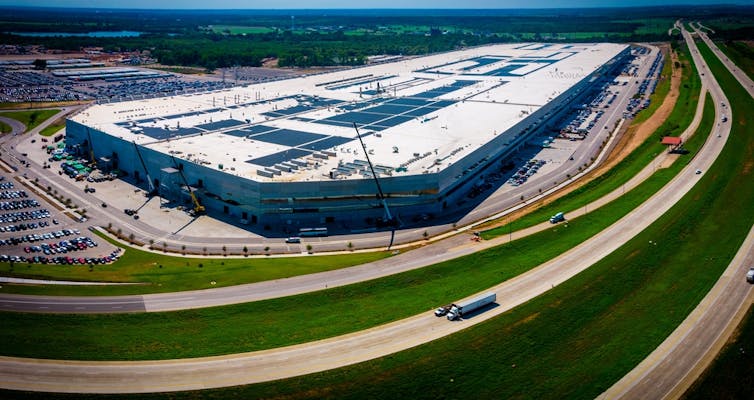
The road ahead
The explosion in global demand for EVs is likely to continue. Countries like China, the US and Germany
have moved faster than the UK to attract and even build the necessary infrastructure and manufacturing capabilities to start trying to meet this demand.
But it seems the UK government hopes to catch up, with the help of the largest “British” car manufacturer JLR (actually owned by Indian group Tata). This is why JLR’s plan to build the largest battery plant in the UK is very welcome news for UK auto manufacturing. Alongside a significant number of jobs, it should finally lead to an increase in British production again, and crucially, meet the new rules of origin for the batteries.
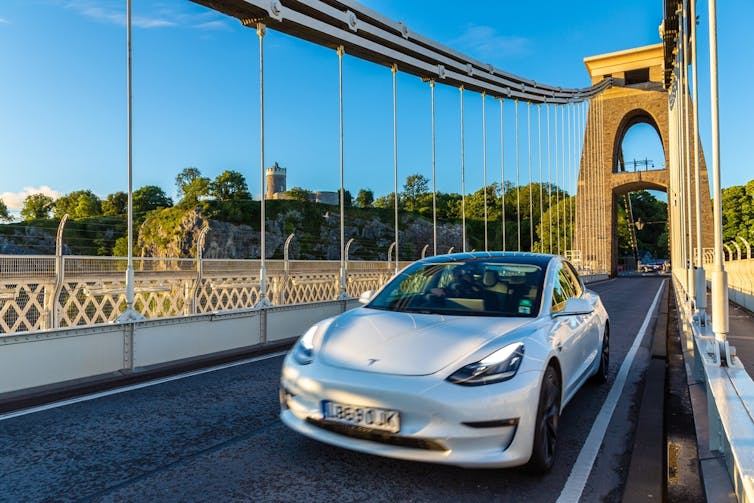
But getting the strategy right will be key. Tesla and China’s top-selling EV manufacturer BYD already have infrastructure set up to build EVs. The Tesla Model 3 and Model Y have seemingly come out of nowhere to rank among the UK’s top ten best-selling cars in just a few years (not just among EVs but all cars). BYD, the largest EV manufacturer in the world could repeat this success having launched their cars in the UK this year.
Rather than establishing its own industry, the UK should woo these manufacturers to set up a British base for production with more battery plants. This could build on the blueprint British car manufacturing already designed with Japanese automakers in the 1980s.
Tom Stacey receives funding from South-Eastern New Energy, an ERDF funded project.